Ladann Kiassat
Science & Technology Editor
3D printing — also known as the additive manufacturing process (AM) — has become a useful tool used by many engineers around the world. Metallic materials that involve 3D printing go through a rigorous process that includes the fusing of fine-scale particles via focusing a laser or electron beam on the given material. Researchers at UC Santa Barbara (UCSB) set out to design alloys that are suitable with the unique additive processing conditions while managing to maintain properties of the given material in demanding environments that are encountered in energy, space, and nuclear applications.
This research was conducted to make high-strength alloys more crack-resistant during the AM process. The UCSB faculty contributing to these research efforts are Dr. Tresa Pollock, professor of materials and associate dean of the College of Engineering, UCSB staff scientists Chris Torbert and Gareth Seward, and UCSB Ph.D. students Sean Murray, Kira Pusch, and Andrew Polonsky.
In collaboration with Carpenter Technologies and Oak Ridge National Laboratory in the Oct. 2 issue of the journal Nature Communications titled, “A defect-resistant Co–Ni superalloy for 3D printing,” UCSB researchers have outlined their findings including a cracking solution via a new class of alloys that hold could advance the use of AM to use in demanding environments.
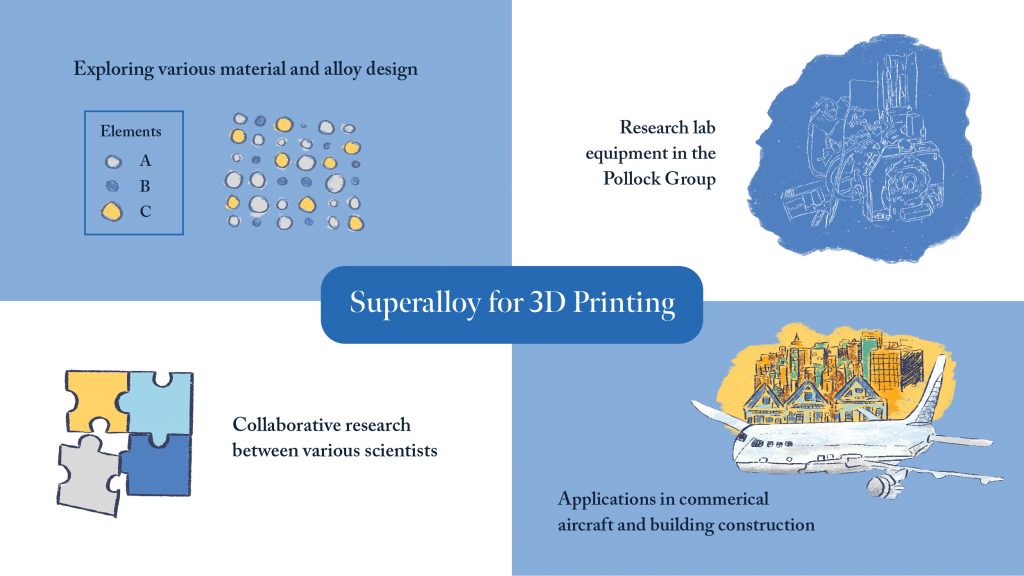
In the paper, researchers describe a new class of 3D-printable superalloy containing both Nickel and Cobalt that are able to maintain their structure at 90 percent of their set melting point in comparison to most of the other alloys that fall apart at around 50 percent of their melting points.
The paper describes the utilization of “Co-Ni alloy compositions that are favorable for AM and also possess favorable mechanical and environmental properties.” The study states, “Ni-base superalloys are the material of choice for their structural components such as single crystal (SX) turbine blades and vanes used in hot sections of aircraft engines and land-based natural gas turbines.”
In an interview with the College of Engineering at UCSB, Pollock explained that “the high percentage of cobalt is what allowed the designing of the features into liquid and solid states of the alloy,” which makes it extremely compatible with a wide range of AM demands. They reached their conclusions regarding this superalloy via extensive research that is highlighted in the hyper-linked academic article above.
“The applications of this new and improved superalloy are tremendous finds in the field of 3D printing. UCSB faculty continues to push the boundaries regarding research in the engineering department.”
Along with Professor Pollock’s new discoveries, this research was done in collaboration with UCSB materials professors Dr. Carlos G. Levi and Dr. Anton Van Der Ven. The research was funded by a $3 million Vannevar Bush Faculty Fellowship which was awarded to Pollock from the U.S. Department of Defense in 2017. This is the U.S. Department of Defense’s most notably renowned single-investigator award, aiming to support the type of research that has an indescribable impact on the world of efficient engineering.
The applications of this new and improved superalloy are tremendous finds in the field of 3D printing. UCSB faculty continues to push the boundaries regarding research in the engineering department. This discovery can lead to advancements made by commercial aircraft, which lead to increased safety of passengers on board. A Co-Ni superalloy, being extremely adaptive to high temperatures, can aid in buildings in California which is notorious for being a state that is prone to wildfires.